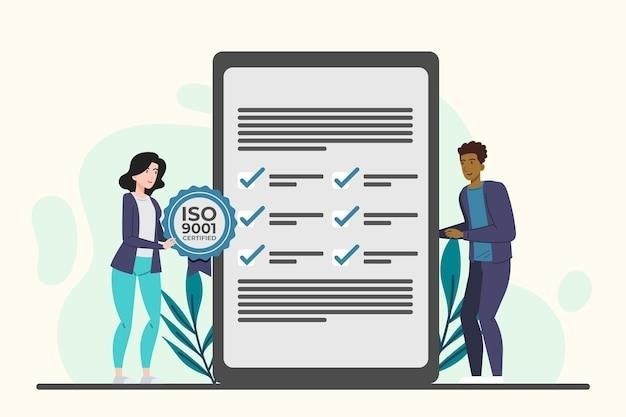
A well-structured work instruction format is crucial for implementing an effective ISO 9001 quality management system. It ensures clear and consistent communication of processes, minimizes errors, and promotes operational efficiency. While ISO 9001 doesn’t mandate a specific format, adopting best practices is essential for creating user-friendly and compliant work instructions.
Introduction
In the realm of quality management, work instructions serve as the bedrock for consistent processes and operational excellence. These detailed documents outline the specific steps, procedures, and guidelines necessary to execute a task or activity effectively. Within the framework of ISO 9001, the international standard for quality management systems, work instructions play a pivotal role in ensuring that organizations operate in a structured and controlled manner.
ISO 9001 emphasizes the importance of documented information, and work instructions fall under this umbrella. They provide a clear roadmap for employees, ensuring that tasks are performed accurately and consistently, regardless of individual skill levels or experience. By standardizing processes through well-defined work instructions, organizations can mitigate the risk of errors, enhance productivity, and ultimately deliver products and services that meet the highest quality standards.
This comprehensive guide delves into the nuances of work instruction format within the context of ISO 9001, exploring its significance, key components, and the benefits it brings to organizations. We will shed light on the essential elements of a work instruction format, from clear and concise language to visual aids and quality checks, ensuring that your organization’s work instructions are not only compliant with ISO 9001 requirements but also readily understood and implemented by your workforce.
The Role of Work Instruction Template ISO 9001
A well-crafted work instruction template serves as the foundation for a robust ISO 9001 quality management system. It acts as a blueprint, guiding organizations in developing clear, consistent, and effective work instructions that align with the principles of the standard. The template provides a standardized structure, ensuring that all work instructions adhere to a common format, making them easily accessible, understandable, and readily applicable across the organization.
The work instruction template ensures that essential elements, such as purpose, scope, procedure, safety precautions, quality checks, and record-keeping, are consistently included in all instructions. This standardization streamlines the process of creating new work instructions, reduces the risk of omissions, and promotes consistency in how tasks are performed throughout the organization. Furthermore, the template facilitates the review and approval process, ensuring that work instructions meet the necessary quality and compliance standards before being implemented.
By leveraging a work instruction template, organizations can significantly enhance their quality management system, fostering a culture of continuous improvement and ensuring that all processes are documented, controlled, and readily available for reference and training. This, in turn, contributes to the overall efficiency, effectiveness, and quality of the organization’s operations, ultimately leading to greater customer satisfaction and a stronger competitive edge.
Steps to Develop ISO 9001 Compliant Work Instructions
Developing ISO 9001 compliant work instructions requires a methodical approach to ensure they are comprehensive, accurate, and effective. The process involves several key steps⁚
- Identify the Process or Task⁚ Begin by clearly defining the process or task for which you need a work instruction. This involves understanding its purpose, scope, and the specific steps involved.
- Gather Information⁚ Conduct thorough research to gather all relevant information about the process or task. This includes consulting subject matter experts, reviewing existing documentation, and analyzing data to ensure completeness and accuracy.
- Develop a Flowchart or Diagram⁚ Create a visual representation of the process or task using a flowchart or diagram. This provides a clear and concise overview of the steps involved and their sequence;
- Write the Instructions⁚ Write the work instructions in a clear, concise, and unambiguous manner, using plain language and avoiding technical jargon. Each step should be detailed and easily understood by the intended audience.
- Include Necessary Information⁚ Ensure that the instructions include essential elements, such as the purpose, scope, materials required, safety precautions, quality checks, and record-keeping requirements.
- Review and Approve⁚ Have the work instructions reviewed by subject matter experts, stakeholders, and management to ensure accuracy, clarity, and compliance with ISO 9001 requirements.
- Implement and Train⁚ Implement the approved work instructions and provide appropriate training to employees on their use. This ensures that everyone understands the process or task and can perform it effectively.
- Monitor and Review⁚ Regularly monitor and review the effectiveness of the work instructions. Identify areas for improvement and update the instructions as needed to maintain their relevance and effectiveness.
By following these steps, organizations can develop ISO 9001 compliant work instructions that contribute to a robust quality management system and enhance operational efficiency.
The Importance of Work Instructions in ISO 9001
Work instructions are a cornerstone of a robust ISO 9001 quality management system (QMS). They play a critical role in ensuring consistent processes, minimizing errors, and achieving customer satisfaction. Here’s why work instructions are indispensable in an ISO 9001 compliant organization⁚
- Standardization and Consistency⁚ Work instructions provide a standardized approach to performing tasks, ensuring that all employees follow the same procedures. This consistency leads to uniformity in product or service quality, regardless of who is performing the task.
- Error Reduction⁚ Detailed work instructions minimize the risk of errors by providing clear guidance on each step of a process. This reduces rework, waste, and potential customer dissatisfaction.
- Improved Efficiency⁚ Well-written work instructions streamline processes, making them more efficient. Employees can perform tasks quickly and accurately, saving time and resources.
- Enhanced Training and Onboarding⁚ Work instructions serve as valuable training tools for new employees. They provide a clear understanding of processes, enabling faster onboarding and reduced learning curves.
- Documentation and Audit Trails⁚ Work instructions provide documented evidence of processes, which is crucial for audits and demonstrating compliance with ISO 9001 requirements. They also create audit trails, allowing for tracking and analysis of process performance.
- Continuous Improvement⁚ Work instructions facilitate ongoing improvement by providing a framework for identifying areas for optimization. Regular reviews and updates can enhance efficiency and effectiveness over time.
In essence, work instructions are not just a requirement of ISO 9001, but a vital tool for achieving quality excellence, streamlining operations, and driving continuous improvement.
Format for Easy Reading
A well-formatted work instruction is not just about meeting ISO 9001 requirements; it’s about ensuring its usability and effectiveness. A clearly formatted document is easily understood and followed, reducing errors and promoting efficiency. Here are some key elements for creating a user-friendly format⁚
- Clear and Concise Language⁚ Use plain language that is easily understood by all employees, regardless of their technical background. Avoid jargon or overly complex terminology.
- Logical Structure⁚ Organize information in a logical sequence, using headings, subheadings, and bullet points to guide the reader through the steps. This makes it easy to locate specific information.
- Visual Aids⁚ Incorporate visual aids such as diagrams, flowcharts, or images to enhance understanding and clarity. Visual elements can break up text and make the information more engaging.
- Consistent Formatting⁚ Use consistent fonts, font sizes, and spacing throughout the document. This improves readability and makes the document look professional.
- White Space⁚ Leave ample white space between lines and paragraphs to prevent overcrowding and enhance readability.
- Checklists and Tables⁚ Use checklists and tables to present information in a clear and concise manner, making it easy for employees to verify completion of steps.
- Review and Feedback⁚ Get feedback from subject matter experts and end-users to ensure that the format is clear and easy to understand.
By following these formatting best practices, you can create work instructions that are not only compliant with ISO 9001 but also engaging, accessible, and user-friendly.
Benefits of ISO 9001 Document Control
Implementing ISO 9001 document control goes beyond simply creating work instructions; it’s about establishing a system for managing all your quality-related documents. This systematic approach brings significant benefits to your organization, including⁚
- Improved Consistency⁚ Document control ensures that all employees are working from the same, up-to-date information, leading to more consistent processes and outcomes. This reduces variations and errors.
- Enhanced Efficiency⁚ By streamlining document management, you reduce the time spent searching for information and ensure that employees have easy access to the necessary materials. This boosts efficiency and productivity.
- Reduced Risk⁚ Having a documented system for creating, reviewing, approving, and distributing documents minimizes the risk of errors and inconsistencies. This helps to mitigate potential quality issues and legal liabilities.
- Improved Traceability⁚ Document control ensures that all changes to documents are tracked, allowing you to trace the history of a document and understand how it has evolved over time. This is crucial for audits and compliance purposes.
- Enhanced Communication⁚ Document control promotes clear and concise communication by establishing a standardized approach to information sharing; This helps to prevent misunderstandings and ensure that everyone is on the same page.
- Continual Improvement⁚ By regularly reviewing and updating documents, you foster a culture of continuous improvement and ensure that your quality management system remains effective and relevant.
In essence, ISO 9001 document control creates a robust framework for managing your quality-related information, leading to improved consistency, efficiency, risk reduction, and overall quality performance.
Leveraging Digital Elements
In today’s digital age, integrating digital elements into your ISO 9001 work instructions can significantly enhance their effectiveness and user experience. These digital tools offer numerous advantages, including⁚
- Improved Accessibility⁚ Digital work instructions can be easily accessed from any device with an internet connection, making it convenient for employees to refer to them anytime and anywhere. This eliminates the need for physical copies and ensures that everyone has access to the latest versions.
- Enhanced Collaboration⁚ Digital platforms allow for real-time collaboration on work instructions, enabling multiple stakeholders to contribute, review, and edit the documents. This streamlines the development process and fosters a more inclusive approach.
- Interactive Content⁚ Digital work instructions can incorporate interactive elements like videos, images, and simulations, making them more engaging and easier to understand. This can significantly improve employee comprehension and retention of information.
- Automated Updates⁚ Digital systems can automatically notify users about updates to work instructions, ensuring that everyone is working with the most current information. This eliminates the risk of outdated or inaccurate procedures.
- Data Analytics⁚ Digital platforms can collect data on work instruction usage, allowing you to track how often they are accessed, which sections are most frequently viewed, and any potential areas for improvement. This data provides valuable insights for optimizing your work instructions and improving overall process efficiency.
By leveraging digital elements, you can create a more efficient, accessible, and user-friendly system for managing your ISO 9001 work instructions, ultimately contributing to a stronger quality management system.
ISO 9001⁚ The International Standard for Quality Management
ISO 9001 is a globally recognized standard that outlines the requirements for a robust quality management system (QMS). It provides a framework for organizations to consistently deliver products and services that meet customer expectations and comply with applicable regulations. This standard is widely adopted by businesses across various industries, demonstrating its value in enhancing quality, efficiency, and customer satisfaction.
While ISO 9001 doesn’t specifically prescribe a rigid format for work instructions, it emphasizes the importance of documented procedures and controlled documentation. The standard encourages organizations to develop a system that ensures the clarity, accuracy, and accessibility of all relevant information, including work instructions. This ensures that processes are well-defined, understood, and consistently followed across the organization.
By implementing ISO 9001 principles, organizations can streamline their operations, reduce errors, and improve their overall performance. This includes ensuring that work instructions are developed, maintained, and readily available to all relevant personnel. By adhering to the ISO 9001 framework, organizations can foster a culture of continuous improvement, leading to greater customer satisfaction and a stronger competitive advantage.